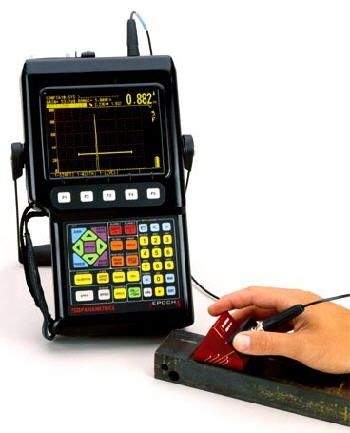
Ultrasonic Testing (UT)
Traditional Ultrasonic inspection uses high frequency sound energy to conduct examinations and perform measurements. Considerable information may be gathered during ultrasonic testing such as the presence of discontinuities, material, or coating thickness.
The detection and location of discontinuities is enabled by the interpretation of ultrasonic wave reflections generated by a transducer. These waves are introduced into a material and travel in a straight line and at a constant speed until they encounter a surface. The surface interface causes some of the wave energy to be reflected and the rest of it to be transmitted. The amount of reflected verses transmitted energy is detected and provides information on the size of the reflector, and therefore the discontinuity encountered.
Ultrasonic flaw detectors are used to find cracks, corrosion, and other safety-critical defects in a wide variety of fabricated and structural metals including bridge beams, aircraft engine parts, railroad rails and axles, steam boilers, oil and chemical pipelines, and storage tanks.